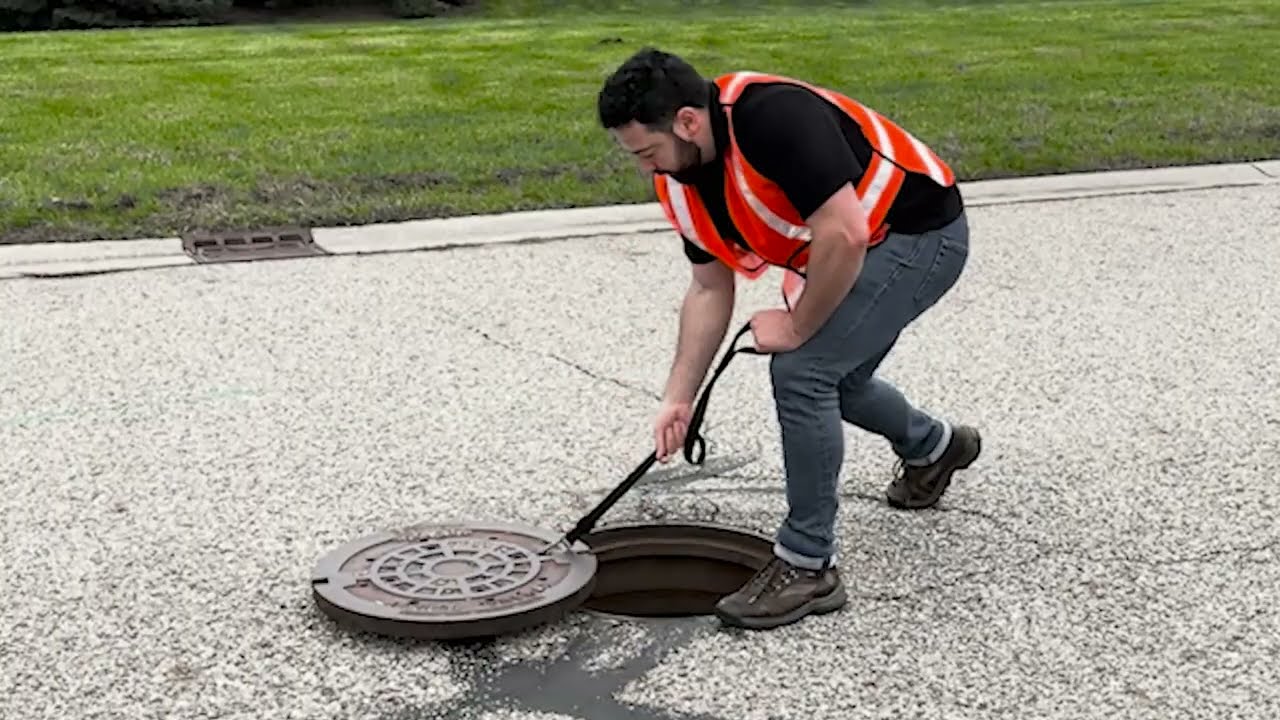
Types of Drain Inspection Chambers
A well-functioning drainage system is crucial for any property, and at its heart lies the humble yet essential inspection chamber. Understanding these vital components can save you time, money, and potential headaches, whether you’re a property owner, contractor, or maintenance professional.
Understanding Inspection Chambers
An inspection chamber, a manhole, is an access point to your underground drainage system. These crucial components allow for inspection, maintenance, and cleaning of drainage pipes without requiring extensive excavation. Modern drainage systems rely heavily on these access points to ensure proper maintenance and longevity of the entire network.
What is an Inspection Chamber?
At its core, an inspection chamber consists of three main components that work together to provide safe and adequate access to underground drainage systems. The design has evolved over decades to meet both practical needs and safety requirements.
Core components of an inspection chamber include:
- Base unit: The foundation that connects to drainage pipes
- Riser sections: Vertical components that extend to ground level
- Cover and frame: The top section that provides secure access
- Sealing system: Ensures watertight connections between components
The chamber’s design allows drainage professionals to:
- Conduct CCTV inspection
- Remove blockages
- Perform essential maintenance
- Clean drainage lines
- Survey infrastructure conditions
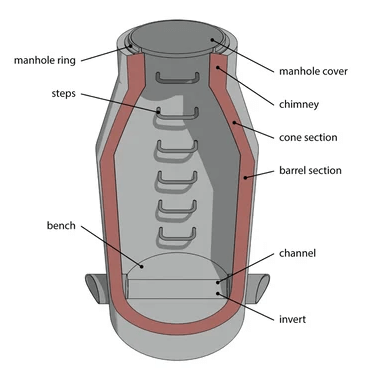
Types of Inspection Chambers
Understanding the different types of inspection chambers is crucial for making informed decisions about your drainage system. Each type serves specific purposes and comes with its requirements and limitations.
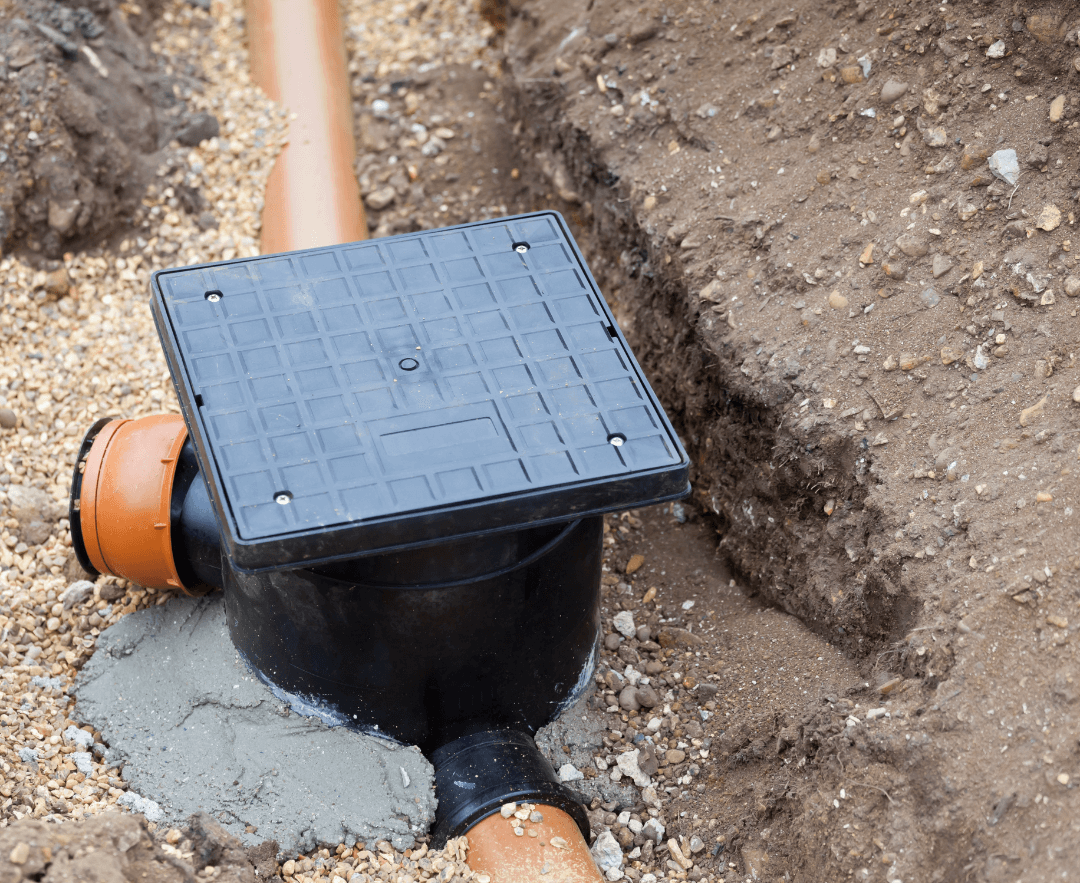
Mini Access Chambers
Mini chambers are the smallest type, designed for residential properties and areas where space is at a premium. These compact units provide essential access while minimising their footprint on your property.
Specification | Measurement |
Diameter | 300mm |
Maximum Depth | 600mm |
Typical Location | Near house/building |
Usage | Residential properties |
These chambers are perfect for:
- Shallow drainage systems
- Individual property connections
- Areas with limited space
- Basic maintenance access
Standard Inspection Chambers
Standard chambers represent the most commonly installed type across residential and commercial properties. They offer an optimal balance between accessibility and practicality, making them versatile for most applications.
Specification | Measurement |
Diameter | 450mm |
Maximum Depth | 1200mm |
Access Type | Equipment only |
Application | Commercial/Residential |
Key benefits include:
- Excellent access to cleaning equipment
- Suitable for multiple pipe connections
- Compatible with standard drain rods
- Greater maintenance flexibility
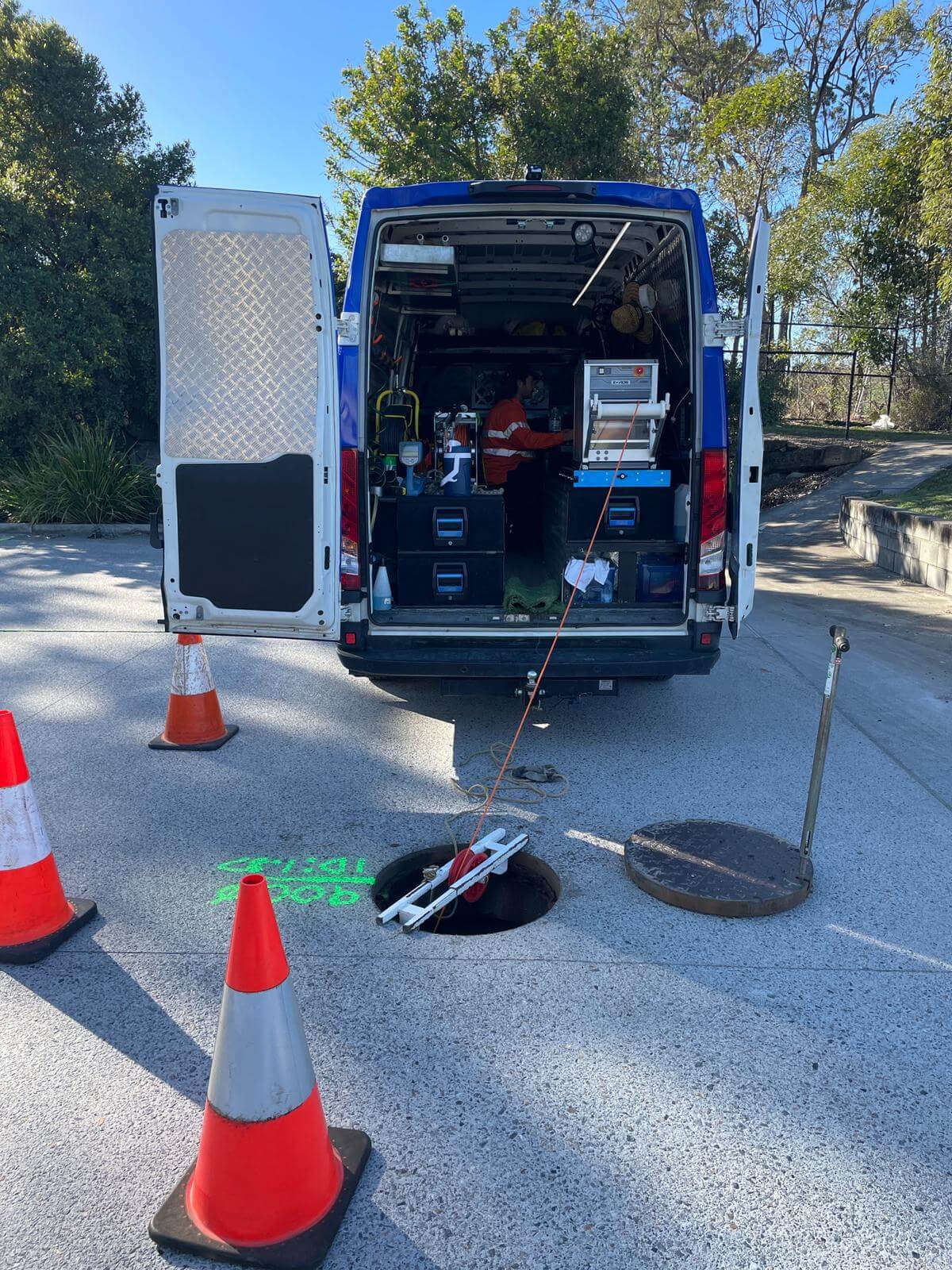
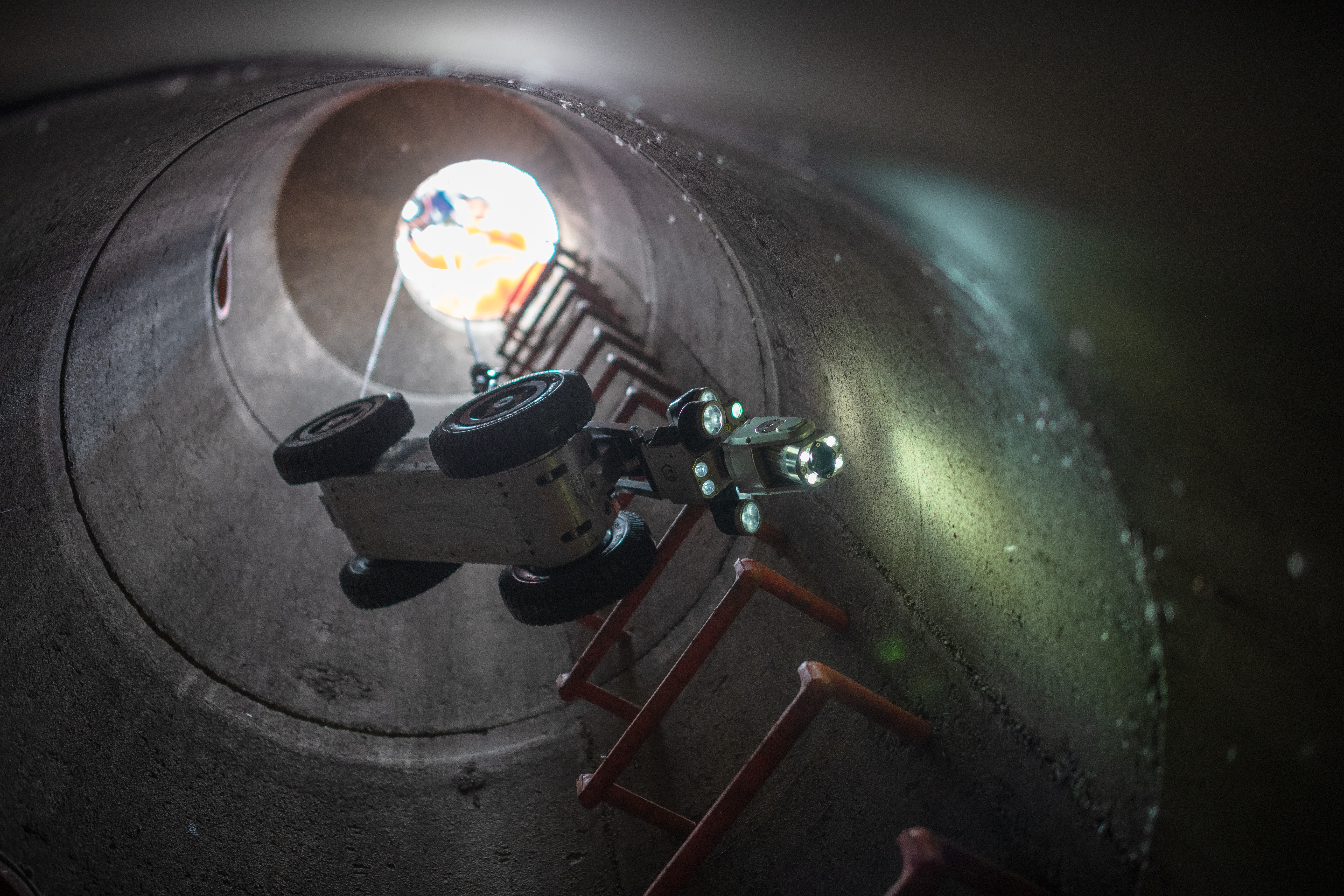
Deep Inspection Chambers
When drainage systems require greater depth, specialised chambers become necessary. These installations demand careful consideration of safety features and access requirements to ensure safe maintenance operations.
For installations deeper than 1.2 meters, special considerations apply:
- Requires reducing rings to limit opening size
- Maximum depth of 3 meters with proper safety features
- Must incorporate ladder access or step irons
- Needs professional installation and maintenance
Installation Guidelines
Proper installation is crucial for long-term performance and safety. A well-installed inspection chamber will serve its purpose effectively for decades, while poor installation can lead to numerous problems and costly repairs.
Site Preparation
Professional site preparation ensures the longevity and stability of your inspection chamber. This crucial first step sets the foundation for a successful installation.
Before installation:
- Conduct ground assessment
- Mark utility locations
- Plan excavation dimensions
- Prepare stable base material
Installation Steps
Proper installation procedures ensure your inspection chamber will function correctly and safely for years.
- Excavate to the required depth plus 100mm for bedding
- Create a level concrete base
- Install base unit and check alignment
- Add riser sections with proper sealing
- Install the cover frame and ensure a level finish
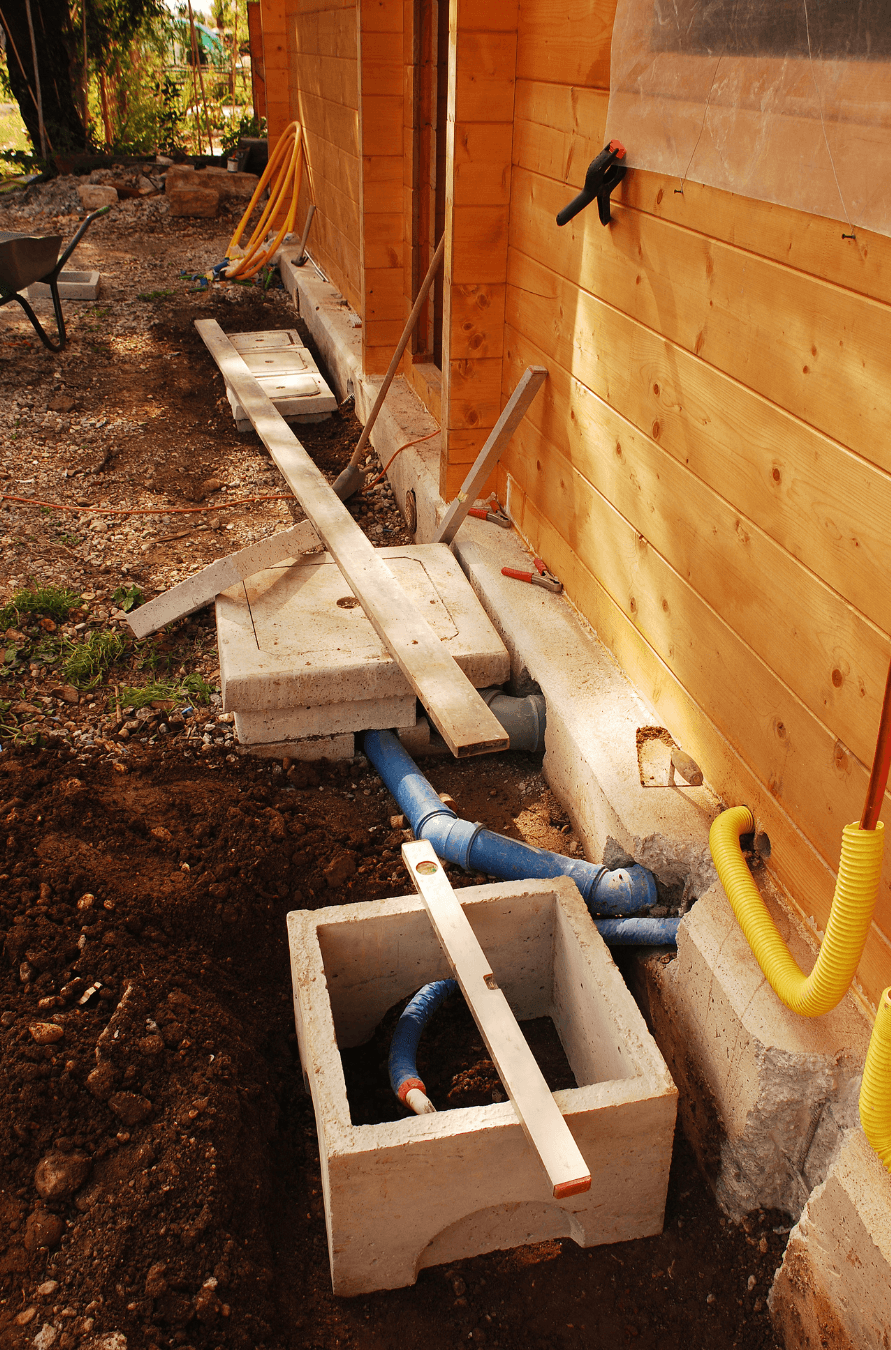
Maintenance and Safety
Regular maintenance ensures optimal performance and longevity. Proper care extends the life of your drainage system and helps prevent costly emergencies.
Maintenance Schedule
A consistent maintenance schedule helps prevent issues before they become major problems:
- Monthly: Visual inspection of covers and surrounds
- Quarterly: Check for blockages and debris
- Annually: Professional inspection and cleaning
- As needed: After heavy storms or suspected issues
Safety Considerations
Working with drainage systems requires careful attention to safety procedures and regulations.
Essential safety measures include:
- Never enter chambers without proper training
- Use appropriate PPE when inspecting
- Check for hazardous gases before opening
- Ensure adequate ventilation during maintenance
Frequently Asked Questions
Q: What is the maximum depth for a 450mm inspection chamber? A: Standard 450mm chambers can be installed to a maximum depth of 1200mm. Beyond this depth, you’ll need unique reducing rings and additional safety features to ensure compliance with regulations.
Q: How often should inspection chambers be maintained? A: Professional inspection is recommended annually, with regular visual checks throughout the year. However, properties in areas with high tree density or prone to stormwater issues may require more frequent inspections.
Q: Can I install an inspection chamber myself? A: While shallow installations might seem straightforward, professional installation is strongly recommended. Proper installation ensures compliance with regulations and optimal system performance.
Q: What are the signs of a damaged inspection chamber? A: Look for:
- Sunken or cracked covers
- Water pooling around the chamber
- Unpleasant odors
- Slow drainage
- Subsidence around the chamber area
Q: When do I need a reducing ring? A: Reducing rings are required for chambers deeper than 1.2 meters to limit the opening size and prevent fall hazards while maintaining access for maintenance equipment.
Q: How do I know if my inspection chamber needs upgrading? A: Consider upgrading if you notice:
- Frequent blockages
- Structural damage
- Age-related deterioration
- Non-compliance with current standards
Choosing and maintaining the right inspection chamber is crucial for your property’s drainage system. Whether installing a new system or maintaining an existing one, understanding these essential components helps ensure efficient operation and prevents costly issues. Regular maintenance and professional installation are key to maximising the lifespan and effectiveness of your drainage system.
Ready to Get Started?
Don’t leave your drainage system to chance. Contact SECA‘s expert team for professional inspection chamber installation, maintenance, or upgrades. Our specialists provide comprehensive drainage solutions tailored to your specific needs. Visit www.seca.com.au to learn more about our services and schedule a consultation.